As the aerospace industry grapples with a “perfect storm” of supply chain issues and material shortages, a panel of experts at the 2024 AMUG Conference shed light on the challenges and potential solutions.
Dan Braley of Boeing Global Services emphasized the situation’s urgency, outlining how geopolitical conflicts, including the war in Ukraine, unrest in the Middle East, and the aftermath of the COVID-19 pandemic, have created severe disruptions. This crisis is particularly poignant for the AM sector, where lead times for critical aerospace-grade raw materials have extended to several months, significantly undermining one of AM’s key advantages: speed.
Laura Macht from the U.S. Army DEVCOM Aviation and Missile Center highlighted the unique challenges faced in sustaining military equipment. With a focus on “out of production spares,” she pointed out the difficulties in obtaining parts for older, often discontinued, military hardware. The issue is exacerbated by the fact that many of these parts exist only as obsolete or non-digital formats, such as 2D hand-drawn designs, complicating their reproduction through modern AM techniques. Macht stressed, “We are in an environment where sustaining older, high-mix, low-volume parts is a challenge, especially when these parts are decades old and vendors no longer exist.”
Hear more from industry experts at our online event Additive Manufacturing Advantage: Aerospace, Space & Defense. Register now.
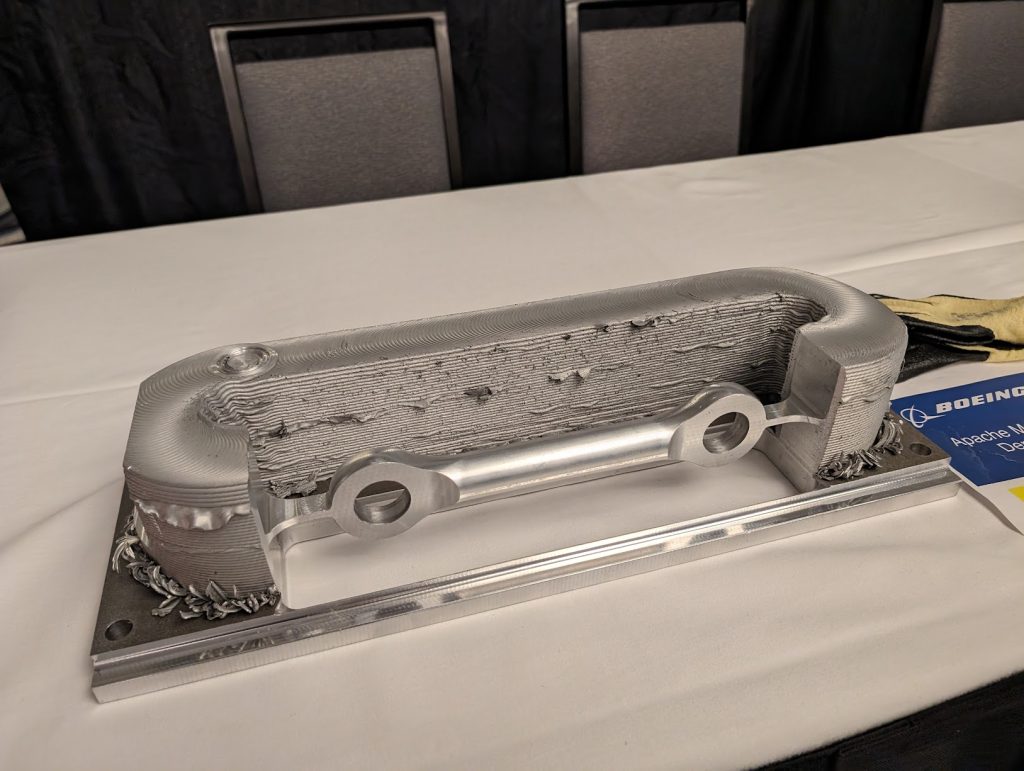
Overcoming Supply Chain Hurdles, Material Availablity and the Need for Unified Standards
Carl Dekker of Met-L-Flo highlighted one scenario with outdated materials and components no longer in production. He noted, “When you get a request for a part, and none of the listed suppliers or materials are manufactured anymore, it’s a serious issue. We can probably make it, but at a crazy price. It’s going to take a lot of work and collaboration.”
Dekker also emphasized the potential impact of collective action by major manufacturers on material availability. “If Boeing, Lockheed, Northrop, and L3 all request the same material, manufacturers might actually listen. But for smaller companies, getting these materials is a significant challenge,” Dekker explained.
Paul Bates from ASTM underscored the importance of standardized qualification processes in AM, especially when each aerospace customer has different requirements. ASTM, an organization that develops and publishes standards, is addressing this by unifying qualification checklists across various sectors, including aerospace, automotive, and medical. Bates said, “There’s a need to make things easier for progression in AM. By unifying standards, we can help get parts built faster and meet customer needs more efficiently.”
Scott Rose from Boeing Research and Technology outlined the diverse challenges faced by Boeing in sourcing and manufacturing aerospace components. Highlighting the complexity of the situation, Rose explained, “We’re dealing with a range of issues, from sourcing hard-to-get parts and materials to grappling with outdated specifications. For example, we sometimes encounter 50-year-old welding specifications or need to deal with the significant cost increase in titanium.” These hurdles span across different Boeing divisions, underscoring the intricate web of standards and materials that must be navigated in aerospace manufacturing.
Braley, also from Boeing, emphasized the urgent need for more efficient design implementation, especially in situations like aircraft on the ground (AOG). He stressed the importance of speed in resolving these issues, saying, “What’s being done in the specs and standards landscape to enable greater AM adoption? Anything we can do faster would help us get aircraft back in the air.”
In response, Paul Bates from ASTM highlighted the efforts being made to streamline and accelerate the standardization process. He pointed out that the development of new standards relies heavily on data, which often takes time to accumulate. Bates stated, “The Centre of Excellence for ASTM in additive has taken on the role of providing guidance and support for research standards. By investing in the development of data, we can accelerate the process of creating new standards.” This approach aims to unify requirements across the industry, facilitating faster qualification of suppliers and enabling more efficient production and repair of aerospace components.
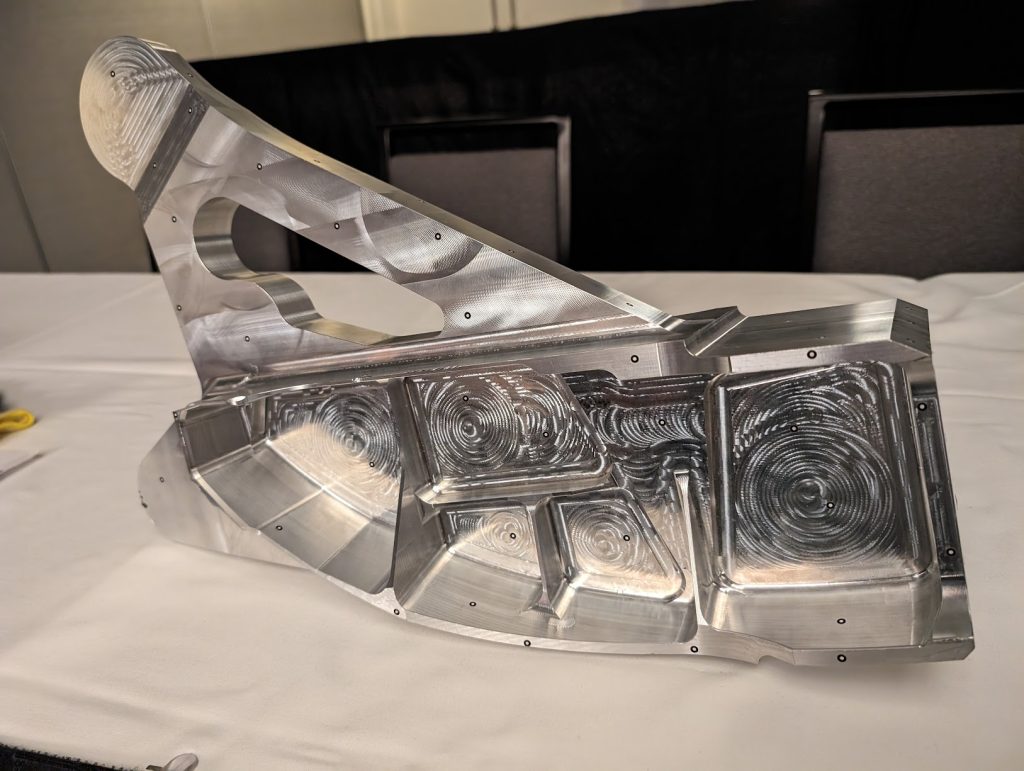
Navigating Additive Manufacturing Standards in Aerospace: Balancing Rigor and Flexibility
Macht from the U.S. Army DEVCOM Aviation & Missile Center voiced a concern regarding AM standards, raising the issue of whether overly stringent standards could become a barrier to AM adoption due to their perceived complexity.
Paul Bates of ASTM acknowledged these concerns, noting the balancing act between being overly prescriptive and not prescriptive enough. He highlighted the consensus-based nature of standard creation, stating, “Standards are created by the industry. If you didn’t join the committee or put your input in, you can’t expect it to be exactly as you want.”
Dan Braley gave some insight into how these standards evolve over time. “It takes iterations of the standards over the years. Some of them have become more restrictive, or companies make their own,” Braley explained.
Finally, Carl Dekker of Met-L-Flo addressed the practical implications of these standards for suppliers to Original Equipment Manufacturers (OEMs). He discussed the challenges of meeting various specifications and the need for open communication with clients. “When we get a request, we evaluate the risk mitigation and put together an approach that encompasses all those specs. If something’s unachievable, we have to go back and say, ‘Here’s your non-conformance report, give us a direction,'” Dekker said.
Aerospace Additive Manufacturing: Seeking a Unified Source of Truth
Laura Macht highlighted another critical issue: “What is the source of truth?” Paul Bates from ASTM addressed this concern, emphasizing the importance of validating data. “If there’s no pedigree behind the data, why are you getting involved with it?” he queried, urging stakeholders to engage with ASTM programs.
Further elaborating on this issue, Dan Braley from Boeing Global Services discussed the necessity of complying with Federal Aviation Administration’s (FAA) regulations and the importance of having detailed understanding and validation from engineering authorities. He noted, “Any new technology going on an aircraft must be well understood. We rely on our stress analysts and work with various committees to ensure data is satisfactory.”
Regarding FAA’s involvement in additive manufacturing or aerospace, there are certainly opportunities for greater engagement. Participants expressed a view that the FAA is maintaining a cautious stance on AM, possibly slowing its adoption in the sector.
Macht shed light on this perception, “It requires us to teach them.” She pointed out that these regulatory bodies are open to understanding AM, but there’s a significant gap in their familiarity with the technology. “What do I need to know about additive? What’s this porosity thing? It’s just new lingo that they don’t know how to look at,” Macht explained.
The panel also highlighted the FAA’s role not as a driver of AM requirements but as an evaluator and assessor of whether existing requirements are sufficient. The discussion suggested that while the FAA is open to new technologies, its conservative approach is more about ensuring safety and compliance than actively promoting AM adoption.
Addressing how new technologies get integrated, it was noted that new technologies are baked into new platforms and step changes come with new programs. This statement points to a more gradual, program-by-program adoption strategy for AM in aerospace, in line with the industry’s stringent safety and performance standards.
Navigating Intellectual Property and Business Challenges in Aerospace Additive Manufacturing
The conversation shifted towards intellectual property (IP) and its role in the industry. Panelists discussed the complexities surrounding IP, focusing on how it affects business decisions and technological advancements.
Laura Macht brought attention to the business perspective on IP, stating, “IP is money. It’s something you can sell as an asset or a service agreement.” She emphasized that while the technology for secure IP exchange exists, the hurdle is often business-driven, with companies viewing IP as a competitive advantage. Macht also addressed the need for different approaches to IP between the Department of Defense (DoD) and commercial entities: “I’d like [the OEMs] to share with me. Is that acceptable? I’m allowed to be selfish, right?”
Another panelist noted the evolving nature of defense acquisitions and how it impacts IP ownership. With changes in how the Air Force approaches procurement, for instance, the landscape of IP rights is constantly shifting.
Carl Dekker highlighted the role of attorneys in the IP process, indicating that the drive for maximization often complicates straightforward agreements. “Attorneys are charged to get everything possible for their client,” Dekker observed, pointing out the influence of legal considerations on business decisions regarding IP.
The panelists collectively acknowledged the need for collaboration and open discussions to resolve these challenges. Macht invited further dialogue on potential solutions, particularly in the context of DoD use, and emphasized the importance of learning from different perspectives to develop more effective approaches to IP in additive manufacturing.
Wrapping up the lively discussion, Paul Bates called for action. “Don’t sit back and complain because you don’t see what you need. Act on it. Join the party,” Bates encouraged, underscoring the significance of active participation in shaping the industry’s future.
The panel concluded with a consensus on the need for open and continuous communication. “It’s amazing how solutions can come when you get the right people talking,” Dekker stated, encapsulating the sentiment of the discussion. The panelists’ call for greater collaboration, sharing of success, and proactive engagement in the AM community underlines a collective effort to overcome challenges and push the boundaries of aerospace additive manufacturing.
For more insights, join our event, Additive Manufacturing Advantage: Aerospace, Space, & Defense.
Subscribe to the 3D Printing Industry newsletter to keep up to date with the latest 3D printing news.
You can also follow us on Twitter, like our Facebook page, and subscribe to the 3D Printing Industry Youtube channel to access more exclusive content.